Casting is the method of making and producing metal parts through different processes. During this process, molten metal is poured or injected into a pre-prepared mold. Then, while the melt cools down at room temperature, it becomes a solid metal, and finally, using processes such as sand blasting and shot blasting to increase the surface quality, the product is made into the desired shape.
Tarikhah, his wife, Jerry
The history of early smelting furnaces in the Iron Age can be traced back to ceramic firing furnaces. From the beginning, skills in model making and mold building were well established. Disposable molds made of sand and clay, wax models, and permanent molds made of stone and metal were used for mass production of casting parts. The interesting thing is that according to the pieces found from previous times, the ability to build hollow spaces and cavities using muscles can be proven.
A variety of casting methods
Types of casting methods for steel
Precision Casting is a method that uses wax for pattern making and this wax is surrounded by a liquid refractory slurry. After pouring the melt into the mold, the wax pattern is destroyed by heating (melts) and an empty space is created for the molten metal to enter inside the mold. Waterglass casting method is a process in precision casting to produce parts made of carbon and alloy steels, whose dimensions are usually small and medium with a smooth surface and close tolerance. This process is one of the cheapest methods for producing steel parts.
Silica sol casting is another precision casting process that is used for a variety of steel alloys, but is also widely used for the production of stainless steel parts. Compared to the waterglass method, it has a much higher cost, but its surface smoothness and dimensional accuracy are unmatched. As a result, for casting steel weighing less than 60 kg, precision casting is the best solution. But for the production of very large parts, sand casting is used more.
Types of casting methods for iron
There are also two main types of processes for producing parts through iron casting. The process that may be heard more is sand casting. Sand casting is a process that uses sand as a mold material. Molds made of sand are relatively cheap and heat resistant enough even for steel casting. In addition to the sand, a material is also mixed with it as a bonding agent (usually clay). Mold holes and channels are created by compressing the sand and directly shaving the sand around models called patterns. This method is used to produce all kinds of iron parts. Most of the iron castings that are done through the sand casting process are gray iron castings and malleable iron castings.
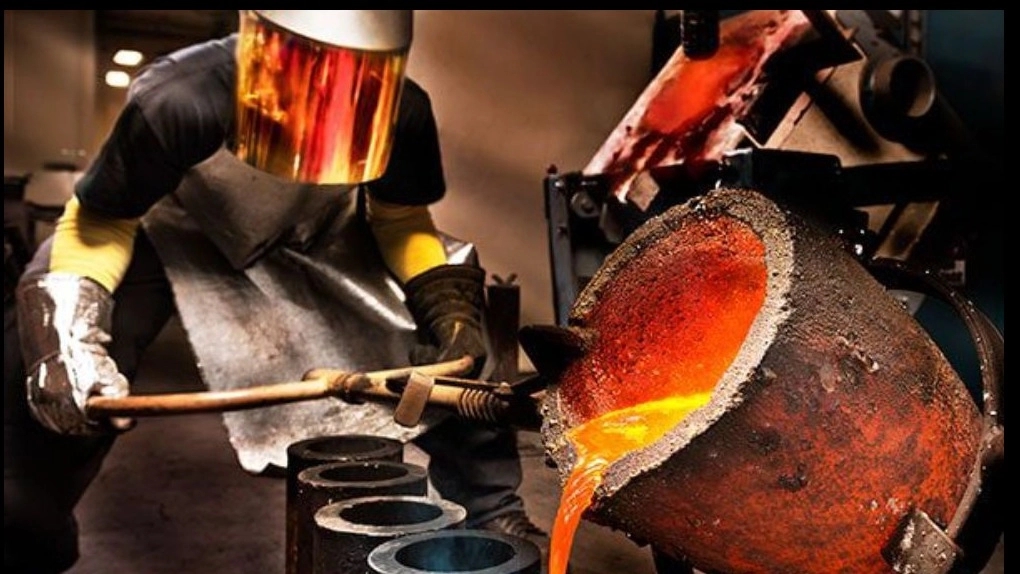
Types of Roche Hi Reichhi Bray Aluminum
Aluminum is one of the popular metals used in various industries due to its light weight. There are also different types of casting methods for aluminum, including: die casting and gravity casting. diecast method is performed at high temperature by injecting melt into high temperature molds, aluminum and zinc alloys. Common aluminum alloys produced by this method are: A356, A380 and ADC-12. Due to the high cost of pressure casting molds, this method is cost-effective for high-volume productions. Also, this process is ideal for casting aluminum parts with thin wall thickness. Gravity casting is used to produce thick aluminum parts. Compared to the diecast method, the final surface is more uneven, but its cost will be lower and affordable. And the machining process is usually done when there is a need for high dimensional accuracy and smooth surface.
The benefits of casting
Habib Elahi Trading is the right choice for you in the field of production and sale of raw materials for metal melting and casting equipment in Tehran.